Vorausschauende Instandhaltung
02.11.2020, 06:01 Uhr
Ausfälle voraussagen mit KI, IoT und Sound
Jede Ausfallminute kann Unternehmen schaden und bedeutet meist finanzielle Einbusse. Innovative Wartungstechnologien setzen nun auf Geräusche als Detektoren.
Wenn Maschinen und Anlagen unerwartet ausfallen, dann kann es für Unternehmen sehr kostspielig werden. So hat 2018 eine Studie von «The Wall Street Journal» und dem Mischkonzern Emerson ergeben, dass ungeplante Stillstände - für die zu 42 Prozent Maschinenausfälle verantwortlich sind - in Produktionsunternehmen Kosten von etwa 50 Milliarden Dollar im Jahr verursachen. Zudem ist so ein Stillstand nach der Wiederaufnahme des Betriebs auch in der Produktionslinie zu spüren.
Deshalb steht Predictive Maintenance bereits seit Längerem auf der Tagesordnung vieler Unternehmen. Laut diverser Studien, unter anderem denen von Roland Berger und BearingPoint, beschäftigen sich etwa 80 Prozent der Unternehmen aus der Industriebranche mit dem Thema vorausschauende Instandhaltung. Moderne Technologien wie IoT und Künstliche Intelligenz eröffnen dabei immer wieder neue Möglichkeiten, Maschinen und Anlagen aus der Ferne zu überwachen und präventiv zu warten. Wozu früher zum Beispiel nur erfahrene Ingenieure und Techniker imstande waren, wird nun mit der sogenannten Sound-based Predictive Maintenance ganz automatisch und rund um die Uhr möglich, nämlich anhand der Geräusche erkennen zu können, ob eine Maschine bald ausfallen wird.
Verräterischer Schall
Die schallbasierte vorausschauende Wartung beruht auf dem Prinzip, dass das Geräuschprofil jeder Maschine einzigartig ist und zudem variiert - je nachdem, ob die Maschine in Betrieb, im Standby-Modus oder im Stillstand ist. Diese Geräusche funktionieren also in gewisser Weise wie ein Fingerabdruck, an dem man nicht nur eine Maschine selbst, sondern auch ihren aktuellen Zustand erkennen kann.
Im Lauf der Zeit kann sich das Geräuschprofil verändern, und genau diese Veränderungen bieten wertvolle Einblicke in die Umgebung der Schallwellen. Verändert sich also das Geräusch - zum Beispiel, wenn ein noch unsichtbarer Verschleiss der Maschinenteile durch die Abnutzung von Lagern oder Wellenversatz entsteht -, kann dies ein erstes Anzeichen dafür sein, dass die Maschine möglicherweise über kurz oder lang ausfallen wird.
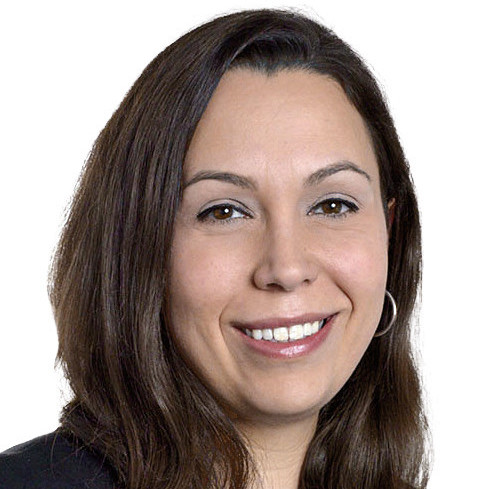
“Rotor- und Lagerdefekte sind die häufigsten mechanischen Fehler, die mit der Analyse des Geräuschprofils erkannt und analysiert werden können.„
Kristina Paralidis, CEO und Mitgründerin von Innsono
Dieser Ansatz erweist sich als besonders effektiv bei Bauteilen, die durch Bewegung Reibungen erzeugen, etwa innerhalb eines Motors. «Rotor- und Lagerdefekte sind die häufigsten mechanischen Fehler, die mit der Analyse des Geräuschprofils erkannt und analysiert werden können», weiss Kristina Paralidis, CEO und Mitgründerin des serbischen Unternehmens innSono, das sich auf intelligente Geräuscherkennung spezialisiert hat.
Die Einsatzmöglichkeiten dieser Art von Predictive Maintenance gehen jedoch über das Erkennen von Defekten in beweglichen Maschinenteilen hinaus. Auch Teilentladungen und Luftleckagen können mittels dieses Ansatzes früh erkannt und schnell lokalisiert werden.