Vorausschauende Instandhaltung
02.11.2020, 06:01 Uhr
Ausfälle voraussagen mit KI, IoT und Sound
Jede Ausfallminute kann Unternehmen schaden und bedeutet meist finanzielle Einbusse. Innovative Wartungstechnologien setzen nun auf Geräusche als Detektoren.
Wenn Maschinen und Anlagen unerwartet ausfallen, dann kann es für Unternehmen sehr kostspielig werden. So hat 2018 eine Studie von «The Wall Street Journal» und dem Mischkonzern Emerson ergeben, dass ungeplante Stillstände - für die zu 42 Prozent Maschinenausfälle verantwortlich sind - in Produktionsunternehmen Kosten von etwa 50 Milliarden Dollar im Jahr verursachen. Zudem ist so ein Stillstand nach der Wiederaufnahme des Betriebs auch in der Produktionslinie zu spüren.
Deshalb steht Predictive Maintenance bereits seit Längerem auf der Tagesordnung vieler Unternehmen. Laut diverser Studien, unter anderem denen von Roland Berger und BearingPoint, beschäftigen sich etwa 80 Prozent der Unternehmen aus der Industriebranche mit dem Thema vorausschauende Instandhaltung. Moderne Technologien wie IoT und Künstliche Intelligenz eröffnen dabei immer wieder neue Möglichkeiten, Maschinen und Anlagen aus der Ferne zu überwachen und präventiv zu warten. Wozu früher zum Beispiel nur erfahrene Ingenieure und Techniker imstande waren, wird nun mit der sogenannten Sound-based Predictive Maintenance ganz automatisch und rund um die Uhr möglich, nämlich anhand der Geräusche erkennen zu können, ob eine Maschine bald ausfallen wird.
Verräterischer Schall
Die schallbasierte vorausschauende Wartung beruht auf dem Prinzip, dass das Geräuschprofil jeder Maschine einzigartig ist und zudem variiert - je nachdem, ob die Maschine in Betrieb, im Standby-Modus oder im Stillstand ist. Diese Geräusche funktionieren also in gewisser Weise wie ein Fingerabdruck, an dem man nicht nur eine Maschine selbst, sondern auch ihren aktuellen Zustand erkennen kann.
Im Lauf der Zeit kann sich das Geräuschprofil verändern, und genau diese Veränderungen bieten wertvolle Einblicke in die Umgebung der Schallwellen. Verändert sich also das Geräusch - zum Beispiel, wenn ein noch unsichtbarer Verschleiss der Maschinenteile durch die Abnutzung von Lagern oder Wellenversatz entsteht -, kann dies ein erstes Anzeichen dafür sein, dass die Maschine möglicherweise über kurz oder lang ausfallen wird.
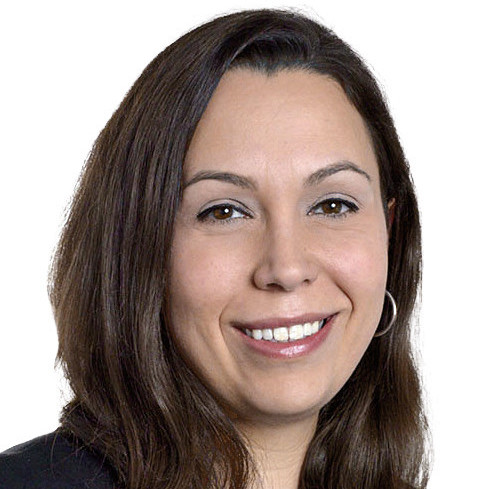
“Rotor- und Lagerdefekte sind die häufigsten mechanischen Fehler, die mit der Analyse des Geräuschprofils erkannt und analysiert werden können.„
Kristina Paralidis, CEO und Mitgründerin von Innsono
Dieser Ansatz erweist sich als besonders effektiv bei Bauteilen, die durch Bewegung Reibungen erzeugen, etwa innerhalb eines Motors. «Rotor- und Lagerdefekte sind die häufigsten mechanischen Fehler, die mit der Analyse des Geräuschprofils erkannt und analysiert werden können», weiss Kristina Paralidis, CEO und Mitgründerin des serbischen Unternehmens innSono, das sich auf intelligente Geräuscherkennung spezialisiert hat.
Die Einsatzmöglichkeiten dieser Art von Predictive Maintenance gehen jedoch über das Erkennen von Defekten in beweglichen Maschinenteilen hinaus. Auch Teilentladungen und Luftleckagen können mittels dieses Ansatzes früh erkannt und schnell lokalisiert werden.
Schonende Implementierung
«Ein Vorteil der akustischen Überwachung ist, dass sie nichtinvasiv und kontaktlos sein kann», betont Nicole Foust, Research-Analystin bei Gartner. Oft reichen in der Tat je nach Fall einfache Mikrofone, die in der Nähe von Maschinen und Anlagen aufgestellt werden, zum Beispiel spezielle Ultraschallmikrofone. «Das ist besonders für einige regulierte Branchen wichtig, wo man beispielsweise die Maschinen nicht manipulieren darf, indem man einen Sensor anbringt», erklärt Foust.
Eine besonders spannende Lösung für die kontaktlose Datenerfassung bietet Noiseless Acoustics. Das finnische Unternehmen hat eine Akustikkamera entwickelt, die die gefundenen Probleme in Echtzeit auf einem Bildschirm visualisiert. Das Gerät, das unter dem Namen NL-Kamera vermarktet wird, hat einen Frequenzbereich, der sich bis auf Ultraschallfrequenzen erstreckt, und dient hauptsächlich zur Erkennung von Leckagen in Stromnetzen und Luftaustritten in Fabrikanlagen.
Andere Szenarien erfordern die Installation von Sensoren, die technisch ebenfalls keine bis minimal invasive Eingriffe erfordern. Neuron Soundware, 2018 von Gartner im Bereich akustische Technologien für Predictive Maintenance als «Cool Vendor» ausgezeichnet, verwendet zum Beispiel spezielle Sensoren, die sich ganz einfach am Gehäuse der zu untersuchenden Maschine anbringen lassen. Sie sind somit auch leicht an andere Stellen zu verschieben, um bessere und genauere Ergebnisse zu erzielen. «So beeinträchtigen die Sensoren weder den Maschinenbetrieb noch die Leistung», erklärt Martin Kuban, CMO des in Prag ansässigen Technologie-Unternehmens.
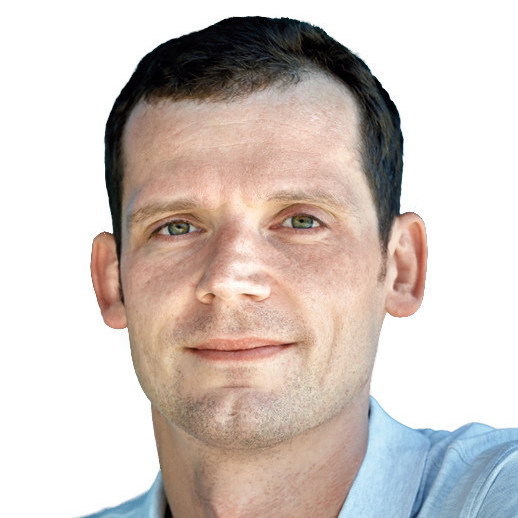
“Sound ist eine der einfachsten und universellsten Methoden zur Erkennung eines mechanischen Defekts.„
Martin Kuban, CMO von Neuron Soundware
Ein weiteres Beispiel für den innovativen Einsatz moderner Technologien bei der vorausschauenden Wartung stellen Analysen dar, die auf Computer-Vision basieren, einer Methode aus dem Grenzbereich zwischen Informatik und Ingenieurswissenschaften zur Interpretation von Kamerabildern. Mit speziellen visuellen Sensoren und einer KI-getriebenen Datenanalyse können Unregelmässigkeiten bei Einzelmaschinen oder Fertigungslinien erfasst werden, bevor es zu Defekten in der kompletten Produktcharge kommt.
So konnte das US-Unternehmen Luxoft für einen führenden Pharmahersteller durch diesen Ansatz den Aufwand bei der Kalibrierung von Dissolutionsgeräten deutlich reduzieren. Früher mussten diese Maschinen für das Testen von Medikamenten durch das Fachpersonal kontinuierlich überwacht werden, damit selbst die kleinste Abweichung in der Kalibrierung sofort korrigiert werden konnte, denn sonst hätten die Tests fehlerhafte Ergebnisse geliefert. Nun werden das Wobbeln und die Rotationsgeschwindigkeit der Geräte durch visuelle Sensoren erfasst und jede Abweichung wird automatisch kalkuliert. Soll ein Gerät nachkalibriert werden, wird das Personal umgehend benachrichtigt. Dieser Ansatz verringert das Risiko menschlicher Fehler erheblich und verschafft den Fachleuten Zeit für andere Aufgaben.
Smarte Datenanalyse
Die Datenerfassung ist jedoch nur der erste Schritt. Als Nächstes müssen nützliche Daten extrahiert und analysiert werden. Dafür werden häufig Machine-Learning- und Deep-Learning-Methoden eingesetzt. «Das Hauptziel dieser Phase ist, ein Muster in Audiodaten zu erstellen, mit dem verschiedene Arten und Bedingungen des Maschinenbetriebs automatisch unterschieden werden können», erklärt Kristina Paralidis. Eine wichtige Grundlage sind dabei die Daten des gesunden Zustands gleicher Maschinen und Anlagen, die unter den gleichen oder sehr ähnlichen Bedingungen laufen.
Damit die KI-Modelle alle auftretenden Geräusche eigenständig korrekt identifizieren können, muss eine umfassende Datenbank von Fehlergeräuschen realer Anlagen und Maschinen vorhanden sein. «Mehr Daten, die unterschiedliche Fehlerzustände der seltenen, atypischen und einzigartigen Betriebsarten darstellen, würden mehr Wissen bringen und bestehende Methoden für die vorausschauende Wartung verbessern», so Paralidis. Deshalb erfordert die erste Phase der Implementierung oft einen menschlichen Input. Die erfahrenen Techniker müssen die auftretenden Geräusche teilweise zuerst selbst bewerten und kennzeichnen.
Sollte es dabei an ausreichend Datensätzen mangeln, können auch andere Methoden angewandt werden. So analysiert innSono auch begrenzte Mengen an Fehlerdaten umfassend und unterstützt KI-Modelle, indem bedeutsame Teile der Audiosignale hervorgehoben werden. Darüber hinaus werden Data-Engineering-Verfahren angewandt, für die nicht zwingend grosse Mengen an Fehlerdaten erforderlich sind. Kristina Paralidis nennt als Beispiel «Techniken, die auf eine autonome Anomalien-Erkennung in einem Datensatz abzielen, wenn diese auftreten, und nicht versuchen, unbekannte Daten in eine der vordefinierten Gruppen zu klassifizieren».
Neuron Soundware wiederum hat sich intensiv mit unterschiedlichen Methoden zur Datenergänzung befasst. Die Überlegung dahinter: Wenn es nicht genügend Fehlerdaten gibt und diese nicht simuliert werden können, dann müssen sie künstlich erzeugt werden. «Wenn die Menge solcher Proben gross genug ist, ist die Messgenauigkeit unter realen Betriebsbedingungen in den meisten Fällen tatsächlich recht gut», konstatiert Martin Kuban.
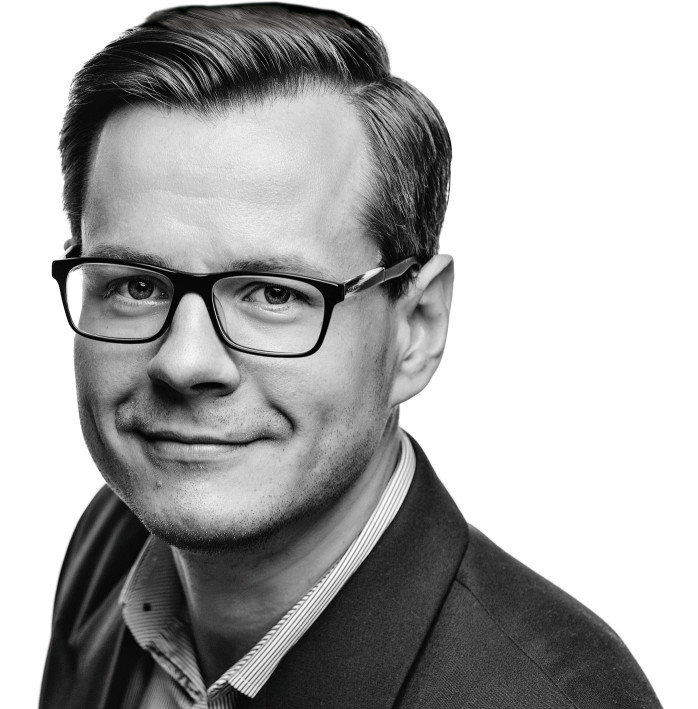
“Sound ist viel mehr als das, was das menschliche Ohr wahrnimmt.„
Kai Saksela, CEO und Mitgründer von Noiseless Acoustics
Auch wenn der Implementierungsaufwand in der Anfangsphase als ziemlich hoch erscheint, können die künftigen Einsparungen es wert sein, wie das Beispiel von Anheuser-Busch InBev zeigt. Der Konzern, bekannt für seine Biermarke Budweiser, wollte testen, ob mittels drahtloser Sensoren, die Ultraschallgeräusche erfassen, vorhergesagt werden kann, wann Maschinen gewartet werden müssen. Im Rahmen dieses Projekts wurden 20 drahtlose Sensoren an drei Motoren der Verpackungslinie installiert. Die aufgenommenen Geräusche wurden mit den Geräuschen eines «gesunden» Motors verglichen, die als Basis für die KI-gestützte Anomalie-Erkennung dienten.
Nach eigenen Angaben hat die Installation der Sensoren im Werk in Fort Collins 20.000 Dollar gekostet - und seit ihrer Bereitstellung ausserplanmässige Unterbrechungen der Produktionslinie sowie Produktverluste von mehr als 200.000 Dollar verhindert. Deshalb plant der Konzern, weitere Brauereien in allen sechs globalen Regionen, in denen er tätig ist, mit den Ultraschallsensoren auszustatten.
Altes Prinzip, neue Technik
Einer der grössten Vorteile der schallbasierten vorausschauenden Wartung liegt in der Präzision und der Früherkennung von Problemen. «Die Daten sind viel dichter und enthalten mehr Informationen, was eine tiefere Analyse ermöglicht», erläutert Kai Saksela, CEO und Mitgründer von Noiseless Acoustics. Bei vielen Messmethoden wird üblicherweise ein Schwellenwert festgelegt, der nicht unterschritten oder nicht überschritten werden darf. Eine Maschine klingt dagegen unter verschiedenen Bedingungen und verschiedenen Lastzuständen unterschiedlich. Während die Überschreitung eines Schwellenwerts auf ein mehr oder weniger unmittelbar bevorstehendes Problem hinweisen kann, kann also die Tonanalyse die eigentliche Ursache des Problems noch in ihrer Entstehungsphase aufdecken - zum Beispiel wenn bewegliche Teile anfangen, aneinander zu schleifen.
Sogar Sensoren für die Vibrationsanalyse sind unter Umständen nicht empfindlich genug, um Probleme frühzeitig zu erkennen. Ultraschallmessungen dagegen können selbst minimale Geräuschanomalien frühzeitig erfassen - früher als Veränderungen in Temperatur und Vibration oder als hörbare Änderungen.
«Ausgefeiltere akustische Überwachungstechnologien können viele Informationen über verschiedene Frequenzbereiche überwachen», erklärt Nicole Foust von Gartner. So kann etwa die NL-Kamera von Noiseless Acoustics in einer Umgebung mit hoher Lärmbelastung, in der Gehörschutz erforderlich ist, kleinste Leckagen auffangen, die selbst in einer völlig geräuschlosen Umgebung kein Mensch hören kann. «Sound ist viel mehr als das, was das menschliche Ohr wahrnimmt», unterstreicht Kai Saksela.
Zwar ist akustische Diagnostik kein neues Konzept. Die Ultraschallmessung etwa wird schon seit über zwei Jahrzehnten zur vorausschauenden Wartung eingesetzt. Mit einem Handgerät stellen Techniker dabei selbst kleine Veränderungen der Frequenz fest. Doch die modernen akustischen Überwachungstechnologien schaffen die Voraussetzung dafür, alle relevanten Maschinen und Anlagen Tag und Nacht zu überwachen - also auch dann, wenn die Techniker sich nicht physisch neben den Maschinen aufhalten können.
Ausserdem steigern sie den Automatisierungsgrad: «Der Einsatz von maschinellem Lernen und Künstlicher Intelligenz ermöglicht es, zu ‚lernen‘, wie ein bevorstehender Defekt aussieht oder in diesem Fall klingt», erläutert Nicole Foust. «Wenn ein bestimmtes Geräusch erkannt wird, wird [automatisch] ein Prozess ausgelöst, der eine detailliertere Überwachung, eine Inspektion oder das Auslösen eines Arbeitsauftrags umfassen kann.»
Fazit & Ausblick
KI-Algorithmen, maschinelles Lernen und Technologien zur Aufnahme selbst kleinster Geräusche über viele Frequenzbereiche hinweg ermöglichen heute, bevorstehende Maschinenprobleme durch blosses Hören präziser als je zuvor, rund um die Uhr und selbst in rauen Industrieumgebungen zu diagnostizieren. «Sound ist eine der einfachsten und universellsten Methoden zur Erkennung eines mechanischen Defekts», unterstreicht Martin Kuban.
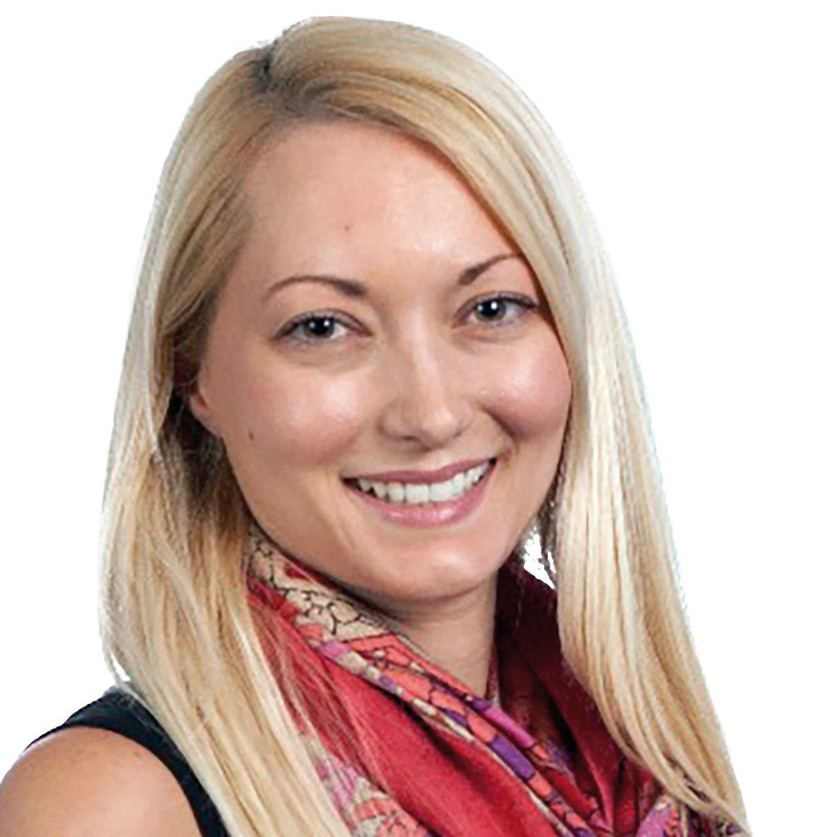
“Ein Vorteil der akustischen Überwachung ist, dass sie nichtinvasiv und kontaktlos sein kann.„
Nicole Foust Research-Analystin bei Gartner
Zwar ist der Markt für die schallbasierte vorausschauende Instandhaltung noch jung, dennoch spricht die wachsende Anzahl der Lösungen und der Unternehmen, die diese Technologie bereits erfolgreich implementiert haben, deutlich für ihr Potenzial. «Immer mehr Unternehmen achten bei der Auswertung von Datenquellen und Technologien darauf, dass diese auch für die akustische Überwachung eingesetzt werden können, um die vorausschauende Instandhaltung womöglich noch effektiver zu gestalten», berichtet Nicole Foust. Auch das Prozessverständnis und die technischen Umsetzungen werden nach Beobachtung der Gartner-Expertin zunehmend ausgereifter. Das steigende Interesse ist nicht überraschend, denn in anlagenintensiven Branchen wird das Anlagenmanagement zu einer Kernkompetenz des Geschäftsbetriebs. Methoden, die eine präzise und frühestmögliche Vorhersage ungeplanter Ausfälle und Stillstände ermöglichen, ziehen deshalb besondere Aufmerksamkeit auf sich.
Von der Sound-basierten Predictive Maintenance profitieren übrigens nicht nur grosse Fabriken. Selbst im Konsumbereich gibt es erste Initiativen. Bei einem innSono-Kunden etwa, einem globalen Hersteller von Haushaltsgeräten, befindet sich die Technologie gerade in der Implementierungsphase. Anhand des aufgezeichneten Tons soll die Zustandsüberwachung eines Kühlschranks anzeigen, ob eine Störung vorliegt und ob alle im Kühlschrank eingebauten Komponenten ordnungsgemäss funktionieren. Noch wird die Technologie nur am Produktionsstandort zur Überwachung der Geräte eingesetzt, bevor diese an die Kunden ausgeliefert werden. Ziel ist es jedoch, die Technik auch den Endkunden zu Hause zur vorausschauenden Wartung der Geräte zur Verfügung zu stellen.