30.11.2007, 08:39 Uhr
Neue Rohstoffe aus alter IT-Hardware
Die Immark in Regensdorf betreibt eine der europaweit modernsten Anlagen für die Wiederverwertung von Elektroschrott. Das Unternehmen gilt als Vorreiterin bei der Automatisierung von Recyclingprozessen.
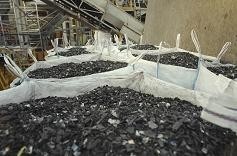
Ruedi Hafner, technischer Direktor der Immark.
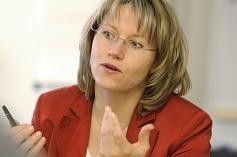
Die Basis für den Erfolg schufen drei Personen: Ruedi Hafner, Gründer und technischer Direktor von Immark, Rolf Jeker, CEO der Immark Gruppe, und Sabine Krattiger, Country Managerin für die Schweiz und seit 15 Jahren bei der Firma. Sie schafften es, die von Ruedi Hafner entwickelten Verfahren für das Elektroschrott-Recycling in Wirtschaftserfolge umzumünzen.
Bereits 1991 nahm die Immark die erste mechanische Anlage zum Recyceln von Kühlschränken in Betrieb, 1994 folgte die erste Anlage für E-Schrott. Damit empfahl sich die Immark Schweizer Grosskunden wie IBM und Unisys, die schon früh mit dem Recyceln begannen, als Dienstleisterin für die Komplettentsorgung ihrer Altgeräte. Denn sie konnte als eines der ersten Schweizer Unternehmen die für grosse Stückzahlen nötige, mechanische Verarbeitung anbieten. Und weil Hafner die Prozesse, für welche er häufig Geräte aus anderen Branchen an die speziellen Recycling-Bedürfnisse anpasste, stetig weiterentwickelte, blieb er immer an der Spitze der Technologie, hatte für die immer neuen Elektrogeräte stets die richtige Technik parat.
Die endgültige wirtschaftliche Sicherheit schaffte aber erst die Einführung der obligatorischen, vorgezogenen Recycling-Gebühr (vRG) im Jahr 2002. Sabine Krattiger: «Bis zur Einführung der vRG bezahlten die Unternehmen für die Entsorgung ihrer Altgeräte. Seither sorgt die vRG für ein wirtschaftlich rentables Entsorgungssystem. Sie sichert auch das Überleben der Immark.» Grund für diese Abhängigkeit: Bis heute deckt der Ertrag aus den Rohstoffen noch immer nicht den Aufwand für die Aufbereitung der ausgedienten Geräte. Trotz steigender Preise für die recyclierten Rohstoffe und trotz immer höherer Automatisierung der Prozesse.
Der Prozess
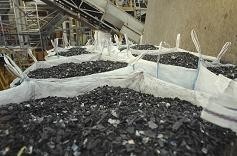
Bei allen Schritten wird Handarbeit heute wo immer möglich vermieden, erklärt Hafner. Das war nicht immer so. Noch vor einigen Jahren war Immark in Arbeitslosenprojekte involviert, kooperierte mit Behindertenorganisationen und Strafanstalten. Doch diese Engagements ermöglichten keine kontinuierlichen Prozessabläufe. Und mit den wachsenden Schrottmengen stiegen auch die Anforderungen an die Mitarbeiter und an die Produktqualität. Den Zeitaufwand für die händische Zerlegung und die hohen Lager- und Transportkosten konnte man sich nicht mehr leisten, die Risiken im Arbeitssicherheits-Bereich nicht mehr tragen. Zudem verlangte die Gesetzgebung des Bundesamts für Umwelt (BafU) und die Kontrolle der EMPA nach mehr Automatisierung.
Interessant: Die Schweizer Gesetze und Vorschriften wurden massgeblich durch die Technologieentwicklungen der Immark mitgestaltet. Sie ist deshalb auch von dem für die vRG verantwortlichen Wirtschaftsverband SWICO und der SENS (Stiftung Entsorgung Schweiz) lizenziert. Das gemeinsame Ziel ist ein möglichst geschlossener Kreislauf bei der umweltgerechten Entsorgung von Schadstoffen und der Rückgewinnung von Wertstoffen in Elektrogeräten.
Der Pioniergeist
Diesem Ziel kommt man langsam aber stetig näher. Beispielsweise hat Hafner grosse Erfolge mit einem an die Recyclingprozesse angepassten «Querstromzerspaner». In ihm wird der E-Schrott schonend zerrissen, ohne dass zuviel Wärme oder Staub entsteht. Zudem können damit erheblich mehr Schadstoffe als bisher extrahiert und so der Anteil zurückgewonnener Wertstoffe erhöht werden. Das Verfahren ist heute weltweiter Recyclingstandard. In Regensdorf hatte der Einsatz des Querstromzerspaners mit einer Kapazität von jährlich 60000 Tonnen Kapazität allerdings zur Folge, dass Immark alleine die so noch stärker automatisierte Gesamtanlage nicht voll auslasten konnte. Daher kam es 2001 zum Zusammenschluss mit Drisa und UGE.
Jüngst hat Hafner ein mehrstufiges Verfahren zum Recyceln von CRT-Bildschirmen umgesetzt. Die Bildschirmgeräte werden zerlegt, das Glas zerkleinert, gewaschen und so die Schwermetalle entfernt. Noch gibt es Verbesserungspotenzial, weil künftig auch die neue Generation von Flachbildschirmen verarbeitet werden muss. Ruedi Hafner: «Das Herauslösen der Schadstoffe aus der Hintergrundbeleuchtung solcher Geräte ist derzeit noch nicht mechanisiert, die händische Demontage der Geräte sehr zeitaufwändig.» Immerhin hat die 2002 in Betrieb gegangene Anlage die Umweltverträglichkeitsprüfung bestanden. Ihr Wirkungsgrad liegt aktuell bei 90 Prozent - vergleichbare Anlagen in Deutschland erreichen erst 37 Prozent.
Dennoch bleiben bei Immark von den jährlich 30000 Tonnen angeliefertem Elektroschrott rund 100 Tonnen Restmaterialien übrig, die teuer als Abfall und Sondermüll entsorgt werden müssen. Hafner arbeitet jetzt an Prozessen zur Aufbereitung dieser schadstoffreichen Kunststoffe, die häufig Schwermetalle wie zum Beispiel Blei, Barium und Brom enthalten. «Das trennen schadstoffarmer von schadstoffhaltigen Kunststoffen ist kein Problem. Vielmehr macht uns die Entsorgung der schadstoffhaltigen Kunststoffe Sorgen», erklärt Hafner. Deshalb wird derzeit in einem Partnerbetrieb in Kanada eine Pilotanlage betrieben, die schadstoffhaltige Kunststoffe in Diesel umwandeln. Hafner ist guten Mutes, dass die Anlage schon 2008 Industriereife erlangen wird. Die ersten Interessenten dafür haben sich bereits bei ihm gemeldet.
Weitere Informationen
Immark Gruppe
Die Aktienmehrheit der 1986 gegründeten Immark ist seit Anfang Jahr im Besitz der irischen Investorengruppe One51, die weltweit mehrere Recyclingbetriebe unterhält. Zur Immark Gruppe in der Schweiz gehören auch die ebenfalls als E-Schrott-Entsorgerin tätige Drisa in Liestal, die Glasverarbeiterin Swiss Glas in Mühlheim und eine Beteiligung an der Kühlgeräte-Recyclerin Kühlteg in Rothrist. Seit dem Einstieg von One51 bei Immark wird die Internationalisierung der Recyclingpionierin vorangetrieben. Heute arbeiten bereits erste Unternehmen in Irland, Deutsch-land, Italien, Frankreich, Kanada und den USA mit der Wiederverarbeitungstechnik der Immark.
Volker Richert, Marco Bischof